Induction Soldering Brass Bellows Assembly
Views Send Enquiry
Objective: To heat a brass bellows and end cap assembly to 450°F for soldering within 20 seconds. Presently, a soldering iron is used to produce the joint between the bellows and cap. The customer requests a quality solder joint with minimal heating of the bellows to prevent annealing and performance losses. Solder preforms, in the form of flat washers, are to be used to complete this application.
Material: Brass Bellows measuring 2″ in diameter
Solder Preforms
Cadmium Free Flux
Temperature: 450°F
Application: The Power of 10KW,10kW output solid state induction power supply along with a unique three (3) turn double wound helical coil was utilized to achieve the following results:
* 450°F was reached and solder flow completed in 6.3 seconds.
* A quality repeatable solder joint was observed.
Equipment: Power of 10KW,10kW output solid state induction power supply including one (1) remote heat station containing one (1) 1.2 μF capacitor, and a unique three (3) turn double wound helical coil with an inside diameter of 0.4″.
Frequency: 307 kHz
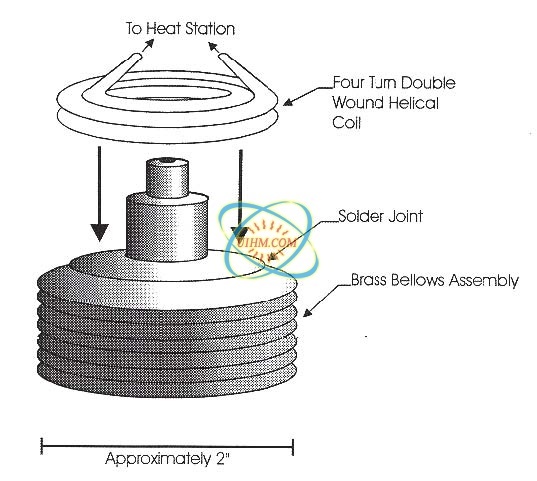
Soldering Brass Bellows Assembly
Related Content
Air Cooled clamp coil (half-open coil) for preheating gas pipeline
induction coating by air cooled clamp induction coil
Remove plastic coating from steel tubes by Induction Heating
Releasing Fixture by Induction Heating
U shape air cooled induction coil by UM-100C-HF for pipeline preheating
induction quenching with custom-design inductor
induction brazing diamond segment
induction brass soldering copper plate_2
Hot
induction brass soldering for copper bricks
induction brass soldering stator ends of wind driven generator within 2 seconds
ultra-high frequency induction brass soldering
induction brass solering_2
induction brass solering_1
induction brass soldering_2
induction brass soldering_1
induction brass soldering
Newest Comment
No Comment
Post Comment