Induction Soldering circuit boards
Views Send Enquiry
Objective To heat post, lead or lead-free solder preforms for various circuit board soldering applications.
Material Upper and lower circuit boards, small and large lead or lead free preforms.
Temperature < 700 ºF (371ºC) depending on the preform used
Frequency Three turn coil 364 kHz
Small two turn coil 400 kHz
Large two turn coil 350 kHz
Equipment •Power of 6 kW induction heating system, equipped with a remote workhead containing two 0.66μF capacitors for a total of 1.32 μF
• An induction heating coil, designed and developed specifically for this application.
Process Three individual coils are used to heat the various locations on the circuit board depending upon if the location is a single application or a group application. The time varies from 1.8 to 7.5 seconds depending upon location. In production the heat stations and coils are moved into position over the post for
automation purposes. Either lead or lead free solder preforms are used. The process time on the lead free solder is slightly longer.
Results/Benefits Induction heating provides:
• Hands-free heating that involves no operator skill for
manufacturing, lends itself well to automation.
• Solder controlled by preforms, no excess left on board.
• Good solder flow without over heating the board and
damaging adjacent circuits and components.
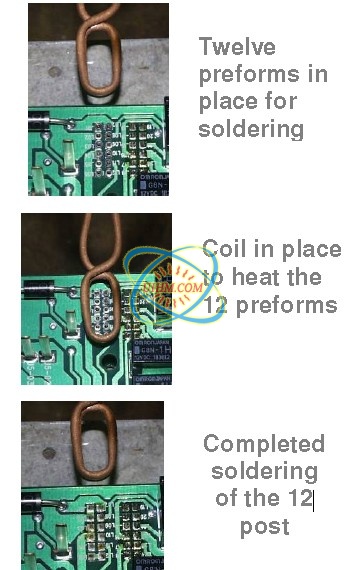
Soldering circuit boards
Related Content
Air Cooled clamp coil (half-open coil) for preheating gas pipeline
induction coating by air cooled clamp induction coil
Remove plastic coating from steel tubes by Induction Heating
Releasing Fixture by Induction Heating
U shape air cooled induction coil by UM-100C-HF for pipeline preheating
induction quenching with custom-design inductor
induction brazing diamond segment
induction brass soldering copper plate_2
Newest Comment
No Comment
Post Comment