Induction Soldering brass
Views Send Enquiry
Objective To solder a brass end cap to a series of copper tubes
Material Preassembled heat exchanger with copper tubes and 2 brass end caps 2.36” (60mm) OD, 0.08” to 0.12” (2 to 3mm) thick at both ends, liquid solder
Temperature 302ºF (150ºC)
482ºF (250ºC)
Frequency 237kHz
Equipment •Power of 30kW induction heating system, equipped with a remote workhead containing one 1.0μF capacitor
• An induction heating coil designed and developed specifically for this application.
Process A dual four turn pancake coil is used to solder 2 brass caps per cycle. Liquid solder is squirted onto the end cap and is heated for 18 seconds at 302ºF (150ºC) to burn off the flux. Then the heat is increased to 482ºF (250ºC) for 15 seconds to solder the parts.
Results
Induction heating provides:
• Even distribution of heating
• Compared to hot plate, induction heating is able to heat two parts in 30 seconds vs. one part in 60 seconds
• Increased production
• No discoloration with the slow heating process
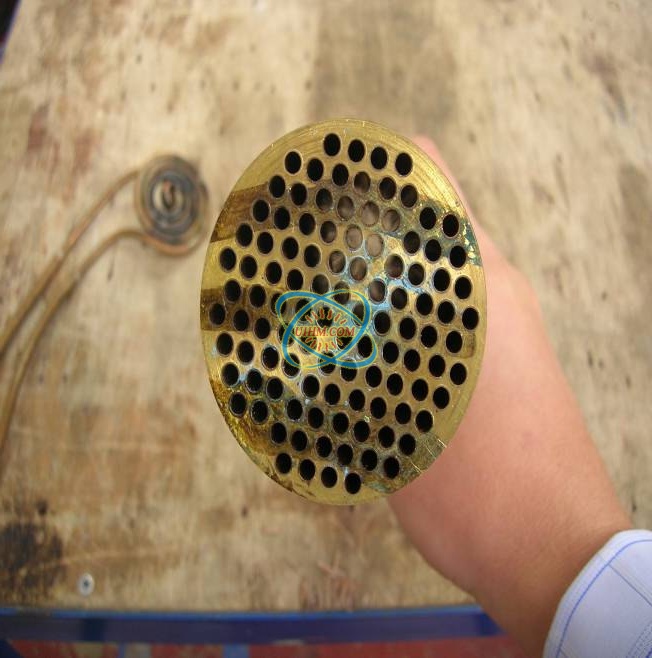
brass end cap
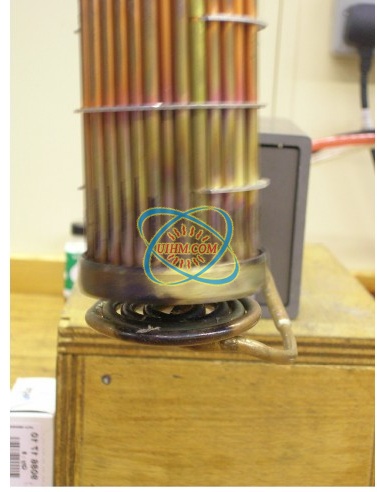
Soldering brass end cap
Related Content
Air Cooled clamp coil (half-open coil) for preheating gas pipeline
induction coating by air cooled clamp induction coil
Remove plastic coating from steel tubes by Induction Heating
Releasing Fixture by Induction Heating
U shape air cooled induction coil by UM-100C-HF for pipeline preheating
induction quenching with custom-design inductor
induction brazing diamond segment
induction brass soldering copper plate_2
Hot
induction brass soldering for copper bricks
induction brass soldering stator ends of wind driven generator within 2 seconds
ultra-high frequency induction brass soldering
induction brass solering_2
induction brass solering_1
induction brass soldering_2
induction brass soldering_1
induction brass soldering
Newest Comment
No Comment
Post Comment