Induction Soldering copper wires
Views Send Enquiry
Objective Soldering two copper wires to pre-installed turrets on a copper buss bar
Material Solder dipped copper/nickel buss bar, 2 tinned stranded copper wires, brazing stick
Temperature 446 ºF (230 ºC)
Frequency 230 kHz
Equipment •Power of 3.2 kW induction heating system, equipped with a remote workhead containing one 1.2μF capacitor.
• An induction heating coil designed and developed specifically for this application.
Process A four turn split helical coil is used to solder the buss bar assembly. The 2 copper wires are applied to the turrets and power is applied for 30 seconds. The brazing stick is fed by hand to the heated parts and the braze flows evenly, creating the joint.
Results/Benefits Induction heating provides:
• Reduced solder time
• Even distribution of heating
• Joint to joint consistency
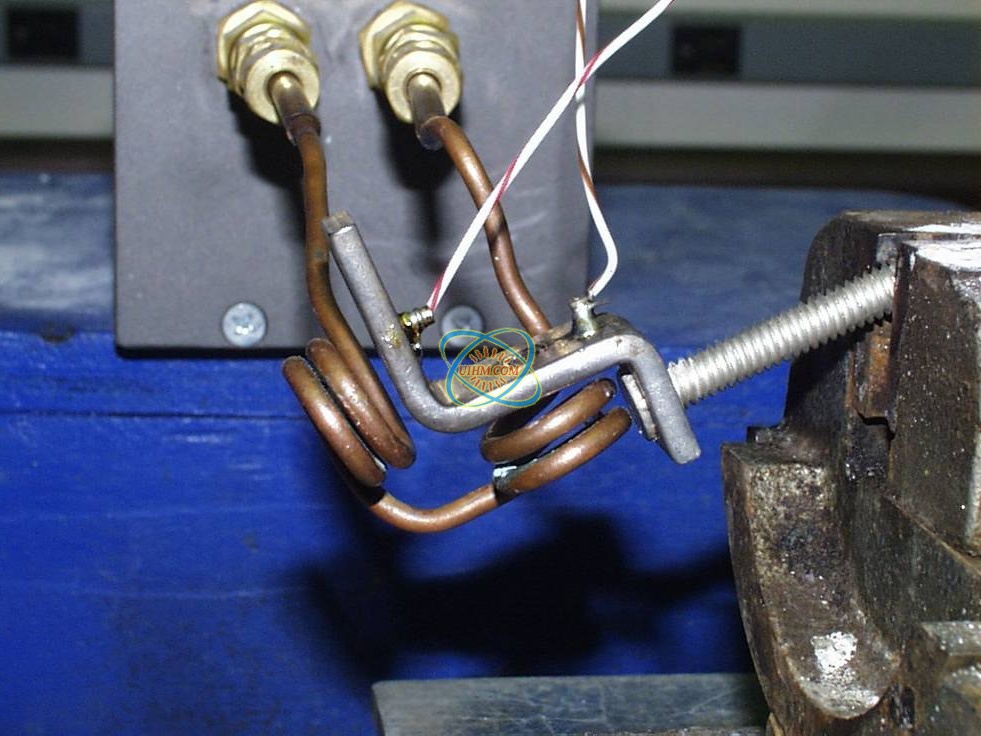
Soldering copper wires to copper bar
Related Content
induction brazing SS steel by handheld induction coil
induction melting silicon and steel
magnesium oxide acidic furnace for induction melting glass
induction preheating gas pipeline by full air cooled clamp induction coil and DSP induction heater
induction melting with Titanium alloy pot by customized induction coil
induction melting aluminium for casting wire wheel
induction heating steel plate by pancake induction coil
induction heating steel knife
Newest Comment
No Comment
Post Comment