Induction Heat seat springs for powder coat
Views Send Enquiry
Objective Heat the steel spring assemblies of automotive seats to powder coat
Material · Steel wire springs ~24” (61 cm) long, 1/8 “ (3.175mm) diameter cross section
Temperature 500 °F (250 °C)
Frequency 57 kHz
Equipment Power of 70 kW, induction heating system, equipped with a remote heat station containing four 1.0 mF capacitors for a total of 1.0 mF
An induction heating coil designed and developed specifically for this application
Process A multi-turn helical coil is wound in a special cross pattern to heat the bottom 1.5 turns of the steel to be coated. This coil efficiency heats the special geometry of the springs. The springs are heated for 10-15 seconds and then soak for another 10-15 seconds before being dipped in the UIHM powder bath. This insures good even flow of the UIHM.
Results/Benefits · Even heating of the spring before dipping provides uniform flow and provides consistent thickness of the nylon coating
· Higher quality end product vs. using an open flame convection furnace. Ovens are sensitive to ambient
temperature and humidity variations and tend to produce uneven results.
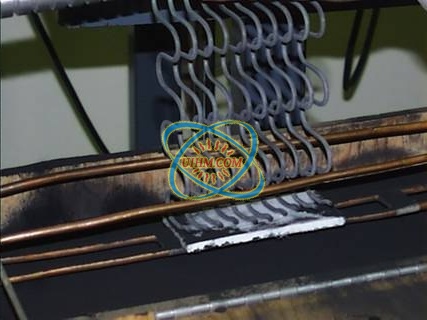
Heat seat springs for powder coat
Related Content
Air Cooled clamp coil (half-open coil) for preheating gas pipeline
induction coating by air cooled clamp induction coil
Remove plastic coating from steel tubes by Induction Heating
Releasing Fixture by Induction Heating
U shape air cooled induction coil by UM-100C-HF for pipeline preheating
induction quenching with custom-design inductor
induction brazing diamond segment
induction brass soldering copper plate_2
Hot
induction heating bolts from turbine
induction debonding from steel rod
induction debonding rubber
Releasing Fixture by Induction Heating
Remove plastic coating from steel tubes by Induction Heating
Induction Heating catheter tipping die
Induction Molding for teflon catheter tip
induction melting for crystal growth
Newest Comment
No Comment
Post Comment