Induction Shrink Fit Cast Iron
Views Send Enquiry
Objective To use induction to prepare cast iron assemblies for shrink fit assembly
Material Customer supplied cast iron rocker arms of varying sizes
Temperature 450 ºF (232 °C)
Process Time 20 seconds
Frequency 48 kHz
Equipment Power of 25kW, 50-80 kHz solid state induction heating system, equipped with a remote heat station containing one 1.0μF capacitor
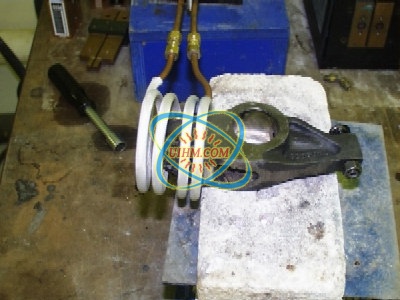
shrink fitting cast iron
An induction heating coil designed and developed specifically for this application.
Process A four-turn helical coil heats the ring at one end of the assembly. The coil is designed to concentrate the field towards the center of the assembly where the thermal mass is greatest.
Across the heated ring, the coil presents a lighter field. After heating, a pin is place within the ring and the assembly is water quenched.
The heat time varies from part to part but is less than 20 seconds.
Results/Benefits Induction heating satisfies the needs of this process for:
• rapid part heating
• flexibility for parts of differing geometries
• individual, series part heating, suitable for automation
• a clean source of heat
• even heat distribution
Related Content
Air Cooled clamp coil (half-open coil) for preheating gas pipeline
induction coating by air cooled clamp induction coil
Remove plastic coating from steel tubes by Induction Heating
Releasing Fixture by Induction Heating
U shape air cooled induction coil by UM-100C-HF for pipeline preheating
induction quenching with custom-design inductor
induction brazing diamond segment
induction brass soldering copper plate_2
Hot
induction shrink fitting motor (stator or rotor)
induction installation (shrink fitting) couplings for Shaft Collar with flexible induction coil
induction shrink fitting wheel
induction shrink fitting stator
induction shrink fitting spindle
induction shrink fitting for rotor and stator
air cooled induction heating for fixing Nuclear Power Unit (loosen screw nut)
induction shrink fitting
Newest Comment
No Comment
Post Comment